|

Pronunciation:
re-vu-LA-shun
Function: noun
Etymology: Middle English, from Middle
French, from Late Latin “revelation-,” “revelatio,” from Latin
“revelare”, to reveal
1a: an act of revealing or communicating
divine truth
1b: something that is revealed by God to humans
2a: an act of revealing to view or making known
2b: something that is revealed; especially,
an enlightening or astonishing disclosure
2c: a pleasant often enlightening surprise.
The truth in music is...
Music is not commensurate with technology, or mechanics, or even
instruments. Music is life. Music is organic. Music is about people.
Music is made by people. Music is made for people. Music is everything
concerning the human experience. Music is living. Music is emotion.
Music is expression. Music is art. Other audio cables do not allow
the listener to experience the true life in music; they sound unorganic,
and — therefore — dead. Revelation Audio Labs cables reveal the organic
truth in music that is the essence of music.
Almost every high-priced, high-end audio cable is derived from off-the-shelf wires, made from inferior metals, extruded in poor insulators, which are the products of machines which are designed to run wire and cable by the kilometer. This very inexpensive wire comes off a gigantic roll from mass manufacturers that make the most common, ordinary wire. The exterior of the cable is dressed up, connectors are installed, and there you have your typical so-called “high end audio cable.” Mass produced, packaged and advertised to have the illusion of high quality exquisiteness. This is the general wire and cable industry infiltrating into the special audiophile cable market. The basic difference between the off-the-shelf cable made by these huge corporations and most high-end music cables boils down to only one thing...the label. The gospel truth is most audio cables are not handmade with exacting attention to detail by craftsmen who have a passion for music.
But this is not so at Revelation Audio Labs! Each and every one of our cables is passionately handcrafted by caring, dedicated artisans, starting with a single bare conductor, and building upon that. Ours are not cables that are run through machines ordained to spew out vast abundance of commodity.
A properly designed audio cable must have excellent solid conductor material, superb noise rejecting shielding, a reasonably low level of capacitance and inductance, and low absorption properties of the dielectric/insulation material. To achieve this level of performance, there are a myriad of factors the cable designer must pay close attention: conductor material, cable geometry, shielding methodology, dielectric absorption, waveform purity, rise and decay time, time smear, inductance, capacitance, AC and DC resistance, wave impedance, reflection factor, and skin effect, to name a few.
The design of Revelation Audio Labs cables focuses most intensely on the three most crucial aspects essential for fine audio cables:
- Conductors
- Dielectric
- Shielding
Conductors: Each conductor is made of
deep cryogenic treated oxygen-free 99.999% (5n) ultra-pure solid
core silver. The silver wire used is made by a company that specializes
in precision high-end audio and RF specific silver wiring technology.
Polished to a totally burr-free and beautiful mirror-like finish,
to exploit 'skin effect' and give the wire as smooth a surface as
possible for optimal electron flow...this wire is so specialized
that each master spool supplied is dated and serialized, and directionality
is indicated by the supplier. This directionality is stringently
retained throughout the assembly process and marked on the exterior
of each cable. Silver is the most electrically conductive metal
(6.29 Siemens/m), and renders the highest performance for transferring
electrons. Pure copper is far less conductive than pure silver;
gold is vastly less conductive than copper. Other conductor materials,
exotic as they may be, are less conductive than pure silver. Lower
conductivity = lower performance. Our silver is 10 to 100 times
(at least a full order of magnitude) more pure than even most so-called
"pure" silver audio cables. Simply put, impurities are a barrier
which hinders electron flow.
What is the objective of other cable makers for using a lesser purity silver? To quote one of their ads: “Because 5n silver (99.999% purity) is rare and on average costs 5-10 times more and very hard to produce and find.” This is obviously a compromise. Well, we won't settle for less for the cause of music, and neither should you. Lower purity silver, used in inferior cable designs, is the main reason silver has the unjustified reputation for having overly exaggerated high frequency response. What is heard is the characteristic hash and noise of the impurities in such material coloring the sound. Only the best conductor material will render the best sonic results. Pure copper, and even gold, is totally inferior to our ultra-pure Cryo-Silver™ in this regard.
Why do other cable makers insist on using copper, while promoting that silver “sounds harsh or bright and lacks bass?” Businesses are driven to be lean and minimize their costs. Obviously the price of copper is only a small fraction of the cost of silver. So, their designers specify copper as their conductor material, and asserting that their enhanced design geometries are the key to “good sound,” in order to employ an inferior conductor material. They do so to lower their cost, at the expense of integrity, and at the compromise of high performance, to elevate their profit margins. To analogize, as the grape is to fine wine, so is wire to fine audio cable. No more can a winery, by means of the wine making process, produce an excellent wine using inferior grapes, than a cable designer, by way of manipulation, produce an excellent audio cable using inferior conductor material. For example, conductor braiding or twisting, used by many a designer as an inexpensive method to improve the sound of their inferior conductor material, inevitably results varying conductor lengths which introduces yet another distortion, “time smear.” Then there are the more elaborate geometries, ever attempting to transform lesser material into a greater consequence. The bottom line is, if there were a better conductor material that our Cryo-Silver™, that would be the material used in our cables. Period. No compromise.
Our Cryo-Silver™ wire is subjected to a precision deep cryogenic process in which the bare solid silver wire is slowly super-cooled (below -315°F below zero), held within 1 degree for 48 hours and then slowly brought back to room temperature at a precisely controlled rate. During the original cooling or solidification phase of the manufacturing process of wire, the crystal structure comprising the wire is in a random, chaotic and haphazard pattern. This random placement causes obstacles for electrons (or the “diodic effect”) when encountered (much like the effects of impurities in the metal). This interference actually hinders electron flow, causing noise and distortion, negatively affecting the coherency of the signal through the wire. At the very cold temperatures (below -315°F) of the deep cryogenic process, the metal crystals align in a more uniform, compact and denser molecular structure through the removal of kinetic energy and inherent stresses. The deep cryogenic process makes a permanent transformation to the entire crystal structure of the metal, not just the surface. The benefits do not deteriorate over time or upon return to ambient temperature. The deep cryogenic treatment effectively eliminates molecular boundaries and drastically reduces the energy separation of molecular orbital valance and conduction bands. The energy levels are so closely spaced that it is very easy for electrons to shift between molecular orbitals and it is extremely easy to add electrons to the molecular bands (form an external source). One should think of a metal that has not been deep cryogenically treated as being open-grained, much like spreading the fingers on one's hand. After being treated, the metal is closed-grained, much like squeezing one's fingers together.
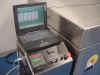
COLDfire Thermal Cycling Machine
Solid core wire technology best deals with wire skin effect. The use of solid core wire eliminates the inherent problem with multi-stranded wire (wire that has a number of strands that are not individually insulated, not insulated from each other). Typically, these bare strands are twisted together and insulated as a whole. Multi-stranded wire is “wonderfully flexible,” but sonically inferior. As electrons travel along such a multi-stranded wire, there is nothing to keep them from “arcing” repeatedly from one strand to another. While this feature is often mentioned as a fault, certain manufacturers have built enviable reputations on disregarding it, using only multi-stranded wire in their illustrious cables. We can get a better perspective on why the fault must not be disregarded if we understand precisely how the electron jumping is detrimental. The main problem stems from the oxide film that covers the metal surface. When it jumps from one strand to another, the signal crosses two oxide boundaries, and worse, “arcs” across a thin air gap. As one strand scarcely touches another, the resistance of this point of contact has a measurable value (especially with copper since copper oxide is not conductive). But the most critical concern is that this point of contact will have semiconductor properties, the same properties that solid state diodes and transistors are designed to have: it affects the signal passing through it by partially rectifying that signal. Thus the musical signal, which may start out as symmetrical AC, moves toward becoming asymmetrical. This effect is subtle, but an interminable number of these “semiconductors” are in a run of multi-stranded wire. With multi-stranded silver wire, this effect is less pronounced—since silver sulfide is conductive—yet still existing. None the less, the air gap is still present, and despite being conductive, silver sulfide still has distinct conductive properties from those of the metal. The same physics apply to multi-stranded wire as to the aforementioned impurities and the crystal grain boundaries within the metal itself, only at a much larger scale. However, with our individually insulated solid silver conductors, these effects are totally avoided.
The wire-connector terminations are solder-free crimps in most of our cable designs. Where soldering is required by connector type, our process provides intimate union of the wire and the contact. The termination is such that the signal is perfectly transferred from wire to contact without first passing through solder. This is an important feature that is rarely contemplated or even understood by most end-users or reviewers. We only use a silver bearing solder which is custom formulated to be both a eutectic low temperature melt and a high conductivity solder, designed specifically for use with our silver wire. The manufacturer of the wire supplies this solder to ensure an almost seamless match when soldering. We only use the state-of-the-art Metcal™ “Smart Heat™” low-temperature soldering process.
The elimination of the most common mode of failure with the audio cable — broken connections — is achieved through several high reliability aerospace industry-standard methods. Sleeving each connection in heat-shrink polyolefin tubing provides stress relief of the connections. Then, the entire internal wiring/connector interface cavity is potted/imbedded using a special compound; literally eliminating damage due to induced stresses. One detail regarding conductor geometry is great care is taken to ensure each conductor is identical in length, eliminating time-based errors. Since the cables are made by hand, the wrapping is slightly inconsistent compared to machine-made cables, and this helps considerably to reduce the cable RF electrical resonances that inevitably distress all cables. (Artifacts of these RF resonances corrupt the audio range, even though the actual resonant frequency can be as high as 10 MHz.) Additionally, each crimp and the wire installed in them is treated with Walker Audio Extreme SST Super Silver Treatment Contact Enhancer during assembly, as is each connector contact pin prior to shipment.
Big Air™ Dielectric:
(patent applied for, Revelation Audio Labs, Inc.): Most common audio
wire has extruded insulation, where the insulation material is in
intimate and immediate contact with the conductor along its entire
length. This forms the dielectric of the wire, which has a tendency
to absorb and release energy to and from the conductor, and is a
function of the capacitance of the cable. The occurrence of this
phenomenon produces negative sonic affects. Dielectric constant
measurements are used to determine the ability of an insulator to
store electrical energy. Common insulator materials and their dielectric
constants are Teflon (2.1), polyethylene (2.25) and polyvinyl chloride
(3.18). The best practical dielectric is air, which has the near-perfect
lowest dielectric constant (1.00059) next to a vacuum (which has
a perfect dielectric constant of 1). However, there is one major
disadvantage of an air dielectric in other audio cables. Although
silver does not react with oxygen at normal temperatures, small
amounts of sulfide, occurring naturally in the atmosphere, tarnish
silver by the formation of silver sulfide on the surface of the
metal. The dilemma of metal exposed to air is far more severe in
the case of copper, which readily reacts to oxygen, resulting in
copper oxide, that is not electrically conductive, on the surface
of the copper metal. Most cable manufacturers that employ an air
dielectric do not address the issue of their conductors being exposed
to ambient air. Some designs actually employ a “porous insulation,”
which seems acceptable in theory, until one considers the aforementioned
affects on the metal surface.
On the other hand, each discrete ultra-pure silver wire conductor, used in all Revelation Audio Labs cables, is hermetically sealed within its own oversized 100% pure virgin Teflon (PTFE) hollow sleeving tube, air being the best practical dielectric, and Teflon being the insulation material with the lowest dielectric constant (2.1). The interior cross section area of the tube is by design many times greater than the diameter of the wire, which minimizes the area of contact of the wire to the insulator. This system provides a huge air dielectric that is unaffected by ambient atmospheric conditions. The resulting characteristically low dielectric constant and extremely low capacitance is responsible for the high propagation speed of our cables.
Shielding: A proven method of shunting
electrical noise from the precious audio electron path. In addition,
especially with power cables, shielding prevents the potential of
EMI and induced eddy currents from detrimentally affecting adjacent
audio system cables and components. We also incorporate Stillpoints
ERS material. Revelation Audio Labs cables are designed with multiple
layers of heavy shielding, comprised of multiple layers of 5 mil.
solid copper, and Mil-Spec helical woven
silver-plated stranded copper braid. The configuration of each shield
layer and the space between the shields
reduce the noise levels dramatically. By incorporating different
shielding techniques and materials, a different spectrum of noise
will be lowered by each shielding methodology and this concurrently
yields the highest level of noise rejection.
Furthermore, each individual conductor pole within our cables
is individually shielded from the others within the shield layers,
through our exclusive Individual Progressive
Hand-Wrap System (patent applied for, Revelation Audio Labs,
Inc.). Silver drain wires common each shield to ground on the source
end only, transferring noise away from the music. Consequently,
the shields are never in the signal or voltage flow path. This provides
a high common-mode rejection of noise and superior resistance to
electromagnetic and radio-frequency interference (EMI/RFI). Our
cables are considerably more shielded than the finest audio cables,
yet, at the same time, are typically more bendable.
One of the highlights of our design, separating ours from all the others:
Ordinary high-end cables are a major path for mechanical vibration
to enter sensitive audio equipment. In addition, the effects resonance
has on the performance of audio cables themselves is well documented.
Audio frequency vibrations induced into the cable may create a state
of microphony and transduce physical resonance into electrical resonance,
polluting the audio stream. To combat this phenomenon, the conduit
of most of our cables is filled with proprietary Ceramic
Micro-Spheres™ (patent applied for, Revelation Audio
Labs, Inc.). This results in a cable that is virtually immune to
the propagation of micro-vibration. This could be one of your most
valuable weapons in your isolation arsenal.
The organic truth in music...revealed. |